Growth and change are essential to success—in life and in business. More and more companies, across every industry and every size of business, are embracing an ethos of continuous improvement: the idea that organizations should aim to make incremental improvements to their services, products, and processes in order to deliver a competitive experience to their customers—and achieve a culture of excellence. In fact, a Deloitte report found that 35% of companies consider continuous improvement a top priority.
The benefits are substantial: McKinsey found that a company engaged in continuous improvement made their product testing process more than 80% faster, while another organization made their assets 20% more productive in under two months. Companies like Amazon, Google, and Toyota have long had this approach coded into their operational DNA—and have seen outstanding results.
Process automation and a culture of continuous improvement go hand in hand.
The benefits of continuous improvement and process automation are similar. Both promote open communication and employee engagement, and both, if executed correctly, can create positive feedback loops: improvement in one area encourages improvement in others. In both cases, deep analysis of current processes, and creativity in considering how to improve them, are key.
What’s more, the team effort—transparency, employee involvement, and knowledge sharing—that goes into bringing process automation to life is itself an act of continuous improvement in practice. Continuous improvement begins with understanding a process in depth, and continues with concerted efforts to make that process more efficient or productive. Process automation takes a similar approach, but focuses specifically on automation as a means of improving processes. Taken together, continuous improvement and process automation can enhance and support each other.
Here, we explore three ways that process automation technology (often called robotic process automation, or RPA for short) can promote an environment where continuous improvement is built into daily work.
Process automation promotes transparency
Transparency is essential to creating a culture of continuous improvement. For companies to set themselves up for better performance, they first need crystal clarity around what they’re doing at the moment. Only when current processes are defined and well-documented can they be refined or improved upon.
Process automation requires a similar devotion to transparency. Before any other work takes place, companies must thoroughly document and map the current state of their processes. This is often an eye-opening moment for leaders and teams, as it immediately reveals a host of opportunities for improvement. The results of the above-mentioned Deloitte survey showed that over 60% of companies were able to make better management decisions based on information revealed through process automation implementation.
In addition to clarifying specific processes, most automation projects require teams to clarify and share broader organizational goals—both near- and long-term—with their automation partner. This exercise promotes transparency amongst all employees, from the C-suite to middle management to frontline workers.
As you prepare to implement process automation, you are, whether you realize it or not, creating an environment of collaboration. Departments which usually work separately will need to communicate with each other about how your systems work and how they could work better. Every aspect of your processes becomes open to discussion—and that’s one of the first steps in developing a culture of continuous improvement.
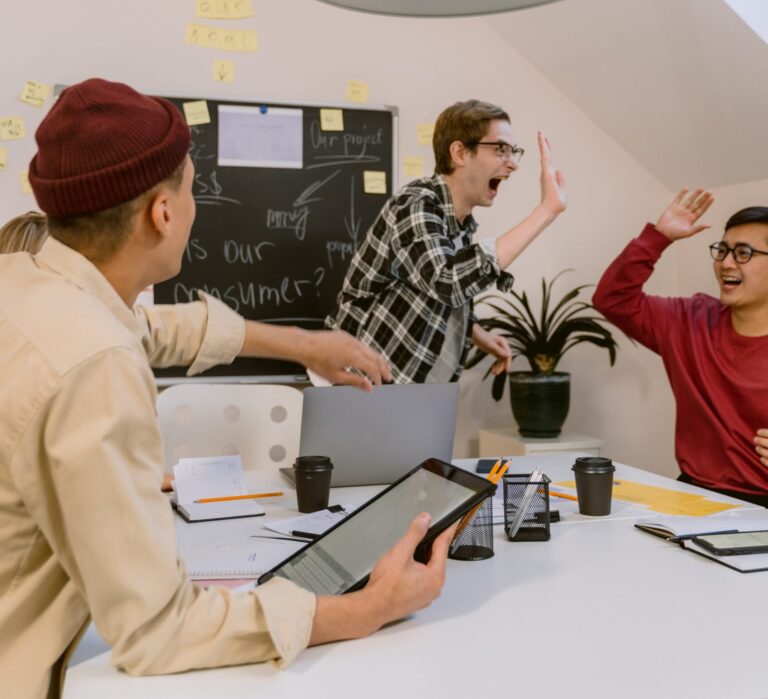
Process automation engages employees
Continuous improvement requires employees to take a more analytic approach to their daily work, asking the question: How can this be done better? Employees who ask such questions must engage fully with their work, viewing it not as a series of boxes to check, but as a process they’re actively involved in, and one in which their own thoughts and opinions play a role.
Process automation, by its very nature, helps foster such engagement. When routine tasks become automated, employees can devote more attention to work that interests them, work that they would like to see optimized and streamlined. But even before implementation is complete, working towards automation by itself can foster such engagement. Effective process mapping requires you to talk to employees on the front lines of the process you want to automate. These employees have the best practical understanding of how the process is currently laid out and its potential to be automated. Their insights aren’t just valuable: they’re essential. According to a McKinsey report, 69% of successful automations involved workers in the early stages.
Importantly, employees who feel like they’re an essential part of the ongoing integration of process automation are more likely to respond positively to such changes. They understand that their jobs aren’t being replaced: rather, they’re being given the opportunity to do more of the work that actually stimulates them, and allows them to contribute to the company’s pursuit of progressive excellence.
Process automation creates a virtuous cycle
When you engage with process automation, you develop a mindset in your workforce that makes further improvements easier and more likely. That’s the first step towards implementing a culture of continuous improvement: employees participating to a greater extent in process improvement in one area are often inspired to look for opportunities to improve processes in other areas.
Continuous improvement is based precisely on this cycle. You begin with the process as it is currently performed. You identify areas where the process could be improved for better productivity, and how you could implement changes to make those improvements. Then you put the changes into practice, observe how they work, and arrive at a new process—which can itself be further improved.
Continuous improvement through process automation
Process automation and continuous improvement are deeply connected, as automation provides an opportunity for your business to cultivate the attitude that drives continuous improvement. The conversations that go into developing automation enable growth, promote employee engagement and satisfaction, and develop deeper ties between various departments—all essential to developing a workflow philosophy that is never satisfied with “the way things have always been done.”
Process automation brings its own challenges, but R-Path has developed a guide to navigating the early stages. For more information, read Establishing a Solid Foundation and Building a High-impact Capability from our Quick Start Methodology.